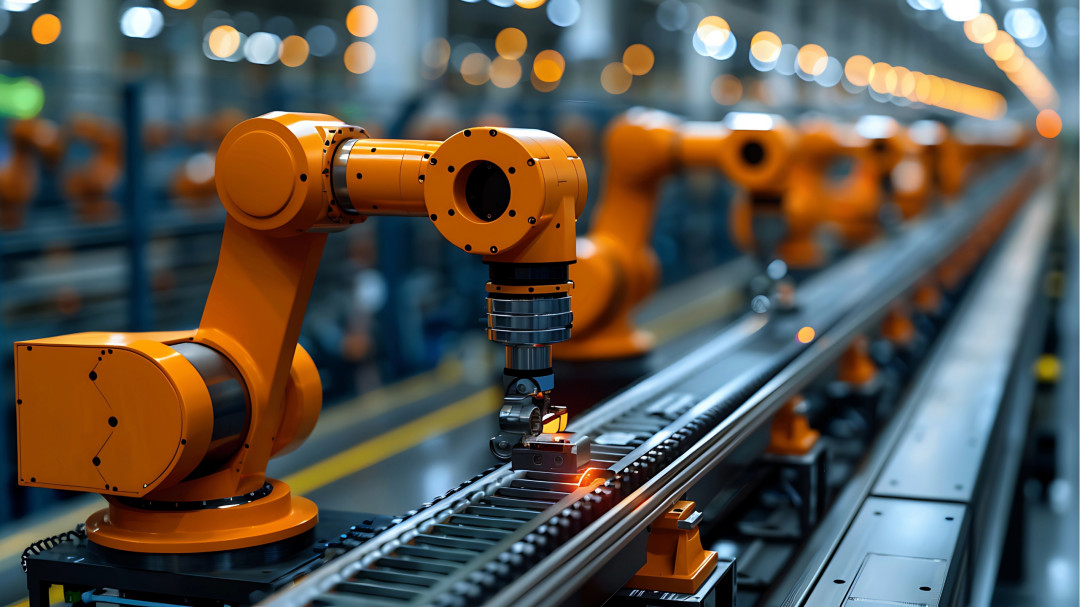
In the new expertise of the Industry 4.0 research advisory board ‘Engineering autonomously changeable Industrie 4.0 systems’, the Fraunhofer Institute for Mechatronic Design (IEM) provides the basis for the next evolutionary step in production system development and identifies concrete areas of action for the future: How are autonomously changeable Industrie 4.0 systems defined in application areas such as logistics or production? Which engineering methods will be used to create them in the future?
Short-term delivery bottlenecks, unplanned machine failures or waves of illness in the workforce: Germany, as a future-oriented production location, has the potential not only to network machines and systems, but also to design them in such a way that they can adapt autonomously to new situations.
‘Digitisation, global uncertainties and competitive pressure are key drivers for the development of networked production systems with a high degree of autonomy and adaptability,’ explains Björn Sautter (Festo SE & Co. KG), a member of the Industry 4.0 research advisory board. ’Such intelligent production systems, with the ability to perform decentralised self-assessment and optimisation in almost real time, enable new performance leaps in the overall system of sustainable production. The expertise describes the contribution that the systems engineering approach can make, the skills required and the key areas for action."
Autonomously adaptable production systems will soon be able to adapt their manufacturing processes to disruptions. By integrating information and communication technologies, data analysis and artificial intelligence, they will offer increased resilience to failures. This will enable companies to minimise risks, adapt to increasing individualisation and complexity and increase their efficiency. While existing production systems are based primarily on simulation, networking and specific machines, autonomously changeable Industry 4.0 systems are characterised by their ability to provide information, flexibility and autonomy.
An analysis of the engineering methods used in production systems shows that there are differences: their manufacturers rely on product development methods, while their users and customers rely on classic factory planning methods. ‘If production systems become even more powerful and complex in the future due to autonomy and changeability, conventional development methods will reach their limits. We therefore call on both industry and political actors to invest in these three areas of action: collaboration between engineering disciplines, further development of engineering methods and investment in knowledge and education,’ explains Prof. Dr.-Ing. Roman Dumitrescu, Director at Fraunhofer IEM and author of the expertise.
In order to meet the challenge of increasing complexity, the expertise evaluates the potential of systems engineering (SE). SE supports the holistic consideration of production systems with interactions between people, technology and organisation and offers methods that actively involve users in the development process. The approach enables interdisciplinary development within a system, thinking beyond the life phases and addressing potential challenges at an early stage.
In production systems, the interdependencies between product, process and production resources are much more complex. However, the further development of SE methods offers opportunities to address autonomy and changeability. The expertise shows the trend in today's industry in four best practice examples: smart factory in toolmaking at KAMAX, ‘factory of the future’ Porsche Zuffenhausen, matrix production in the flow of Siemens AG and Datenfabrik.NRW.
The gap between research and industrial development practice remains large. A competence radar summarises personal, social, technical and methodological competences for the engineering of autonomously changeable Industrie 4.0 systems. The expertise provides concrete recommendations for industry, science and business for the three overarching fields of action: collaboration between engineering departments, further development of engineering methods and investment in knowledge and education.