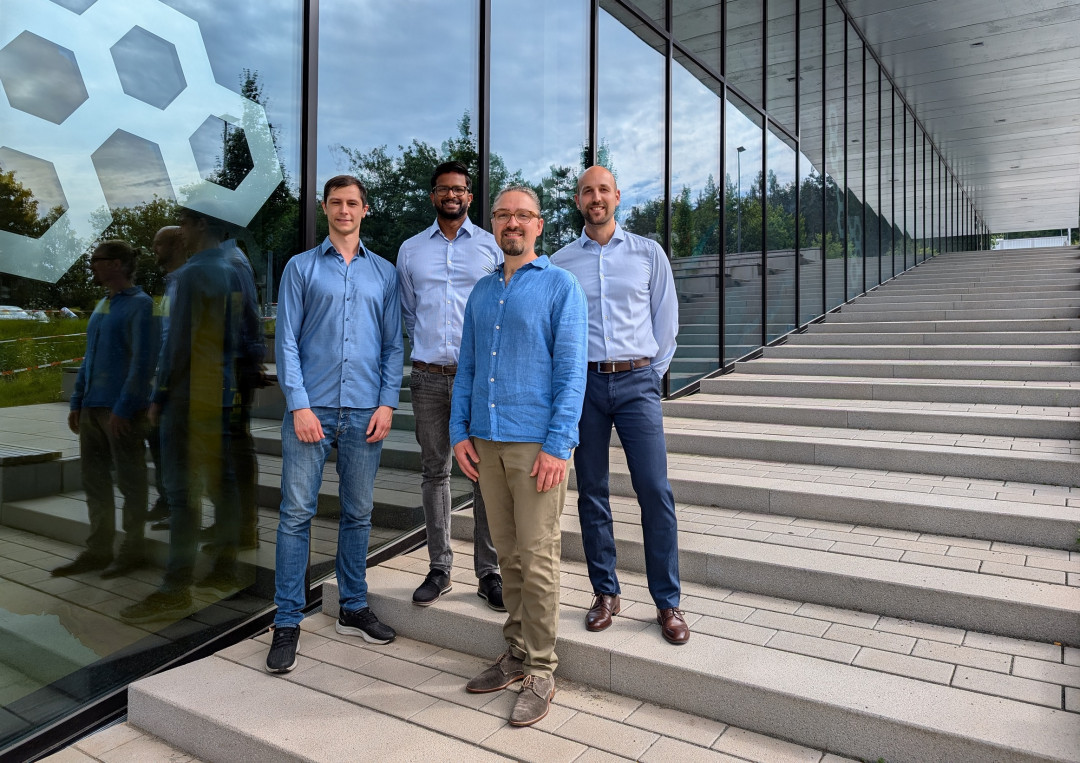
In metal cutting, products with complex geometries are often in demand – this places high demands on production. With a simultaneous shortage of skilled workers and the outflow of expertise, there is a risk of losses in production efficiency and quality. To counteract this, four engineers are developing a software solution in the ‘Refactum’ research project that digitises and links data on past orders and provides decision-making support for the preparation of offers, set-up plans and machine code. The team, which is bringing its system to market maturity at the RPTU, is being funded by the Federal Ministry for Economic Affairs and Climate Protection and the European Social Fund as part of the EXIST programme.
‘Experienced specialists in metalworking companies often know at first glance at a technical drawing which of their production machines can be used for manufacturing,’ says Keran Sivalingam of Refactum. ’And they can assess when a compromise between production costs and product quality is the best solution to achieve a reasonable price-performance ratio.’
But how can this knowledge be secured for the future? To do this, Refactum digitises and links existing information that is distributed across multiple data silos in companies. This includes order data, associated technical drawings or CAD models, calculations and the machine code (NC code) that contains the parameters for setting the production or machine tools. ‘When a new order is received with a technical drawing or CAD model, the employee can have the workpiece analysed and receive all the information needed for production via the software user interface as a decision-making aid,’ explains the industrial engineer.
The software solution thus functions like an elephant's memory and makes suggestions for calculating offers, preparing work, setting up and the machine code. Refactum receives test data and feedback for the development of the system from the field – particularly regarding functionalities and the user interface. What potential do the participating companies see? ‘Particularly in times when there is a shortage of skilled workers, the digitisation of expert knowledge is clearly the main advantage in ensuring competitiveness and the continued existence of the company,’ says Sivalingam. ‘In addition, our software can be used to accelerate work preparation as well as the entire manufacturing process, giving employees more time for important activities.’
In the long term, Refactum aims to enable even more decision support: the software is designed to identify the most suitable production machines in each case to reduce throughput times in manufacturing and to increase efficiency even further. The technology is not only intended to benefit the machining industry. Refactum also aims to integrate upstream and downstream metal processing operations, such as foundries or surface treatment. The ultimate goal is to establish a cross-company production network based on the use of the software.