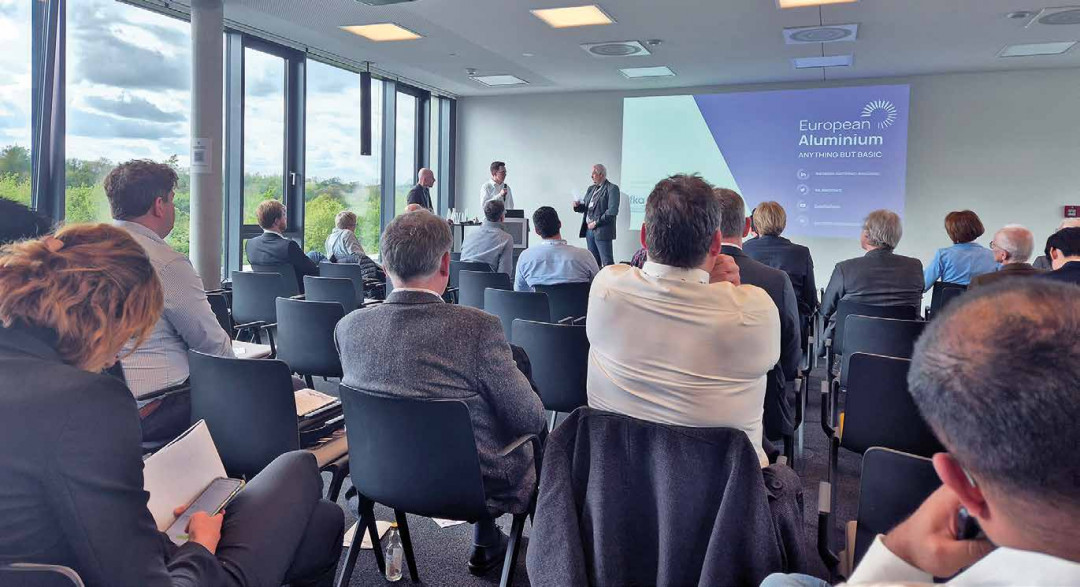
Around 80 participants attended the AMAP forum in Aachen from 25 to 26 April. MAGMA GmbH provided the premises for the event. The invitation was issued by Dr.-Ing. Peter von den Brincken and Dr.-Ing. Uwe Knaak, both managing directors of AMAP GmbH – the Aluminium Cluster at RWTH Aachen University.
The event was opened by three keynote speeches. The first topic was the economic and political outlook for the German and European aluminium industry. This was followed by scenarios for the decarbonisation of the industry. The first block was rounded off with a presentation of global trends and challenges for the environment, technology and society.
One of the highlights of the forum was the panel discussion, in which further details were elaborated. The participants agreed that decarbonisation is the greatest challenge. Here, the processes must run smoothly and at the same time a great deal of research and development work is required. Recycling has enormous potential – the focus is particularly on the recycling of pre-consumer scrap – although the sorting of aluminium is a challenge. It is better to keep materials in circulation, which is also beneficial for the supply chain. In addition, the willingness of car manufacturers to recycle is important; Audi was mentioned as an example, whose models already contain 10 per cent post-consumer scrap.
The industry is investing in green technologies, but there is disagreement about what can be defined as ‘green’ and how much consumers are willing to pay for more environmentally friendly products. One option is the product carbon footprint as a simple criterion. But even with ‘green mining’, there are discussions, and a too narrow definition could prevent alternative solutions for decarbonisation. The ‘green’ label must be validatable, otherwise every company in the market will say: ‘We are green.’ A third party, such as the TÜV, is needed for certification. Since consumers are reluctant to pay a premium for more environmentally friendly products, there was agreement that the legislator must be the driver of the transformation, but that the population must also be involved, since ultimately it is they who have to pay the premium.
The panel was followed by the presentations: in the session on aluminium casting and heat treatment, Magdalena Novak-Coventry (Toyota) described how the production of a die-casting tool using 3D printing takes at least a week. She emphasised the importance of partnerships in bringing innovations to market maturity. She said that the collaboration with Magma was extremely productive, with the company providing support in the design and quality check of the cast workpieces. Another session was dedicated to the topic of sustainability and the circular economy in the value chain. Dr Christian Schwotzer, group leader of the working group on renewable energies and low-carbon process heat at the IOB of RWTH Aachen University, emphasised the importance of sustainability in his presentation. He explained in detail the technological and economic potential of decarbonisation. The fact that studies constantly change their research focus is exciting for science, but it makes it more difficult for companies to make management decisions. They therefore have to be flexible in the transition period from fossil to green.
On the second day of the AMAP forum, the spotlight was on innovations in metallurgical processes and production technologies, among other things. Martin Fieweger (Managing Director of AMEPA – Angewandte Messtechnik und Prozessautomatisierung GmbH) presented technologies for the online measurement of surface roughness and oil film thickness. The more complex design of automobiles means that higher demands are placed on sheet metal surfaces and forming processes. Optical measuring systems can visualise possible distortions on the material.