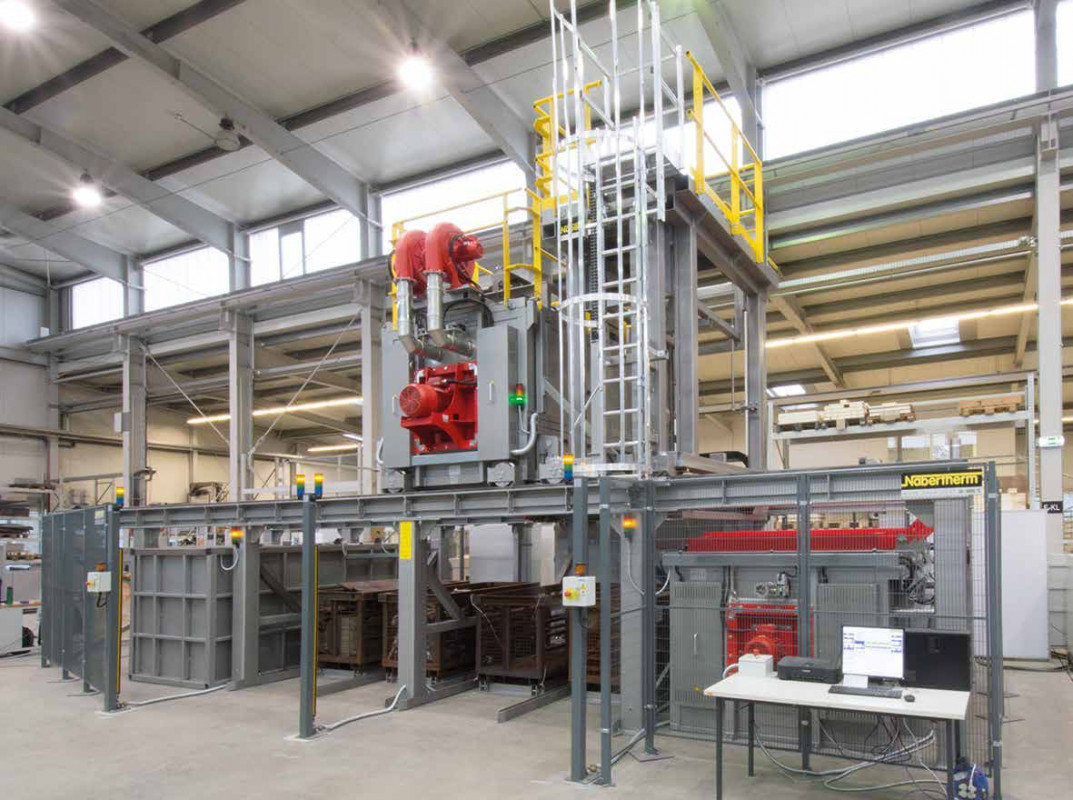
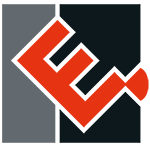
Nabertherm, a leading manufacturer of industrial furnaces, presents a wide range of solutions developed and manufactured for a variety of applications. Nabertherm sets standards with the world's most comprehensive and diverse range of furnace products. Through professional engineering and the use of its production facilities in Germany, the company is able to design customised heat treatment systems that are precisely tailored to the individual requirements of its customers. Many applications can already be covered using the standard furnaces. Customised system solutions are available for complex thermal production processes, enabling efficient implementation.
The company presentation at EUROGUSS will focus on Nabertherm's innovative solutions for die casting and the associated process chains. The ultra-modern electrically heated melting and ladling furnaces are characterised by outstanding melt quality and high melting performance combined with optimum energy efficiency. The tilting furnaces from Nabertherm prove to be an extremely flexible solution for both pre-melting and direct casting into larger moulds. The optimised pivot point enables uniform and precise casting. An integrated safety system, which continues to operate the furnace at reduced power if the thermocouple breaks, prevents the melt from solidifying.
Nabertherm also offers a wide range of furnaces and furnace systems for heat treatment processes before and after casting. Air circulation furnaces from the NA../65 or NA.../85 series are often suitable for preheating or post-heat treatment. These convection ovens are used for temperature ranges below 850 °C and are characterised by their good temperature uniformity. Thanks to the proven option concept, these ovens can be optimally adapted to the desired process, making them very flexible to use. For example, a component can be annealed in the furnace with excellent stress relief, as the controlled cooling not only realises a linear heating curve but also a linear cooling curve.
Drop shaft furnaces, for example, are particularly suitable for solution annealing and the subsequent rapid quenching of aluminium alloys. For thin-walled aluminium components in particular, extremely short delay times of up to 5 s can be achieved, starting with the opening of the door through to complete immersion in the water bath. The drop shaft furnace is mounted on a substructure, which places the quenching bath directly under the furnace. To carry out the quenching process, the base moves horizontally to the side while a basket containing the components is lowered into the quenching bath. The movement technology can be controlled either automatically or semi-automatically.
The combination chamber furnaces N 200/DB to N 1000/14 DB were developed especially for debinding and sintering processes, for example in additive manufacturing. These furnaces can be combined with different debinding packages to ensure efficient and safe process control from simple to professional applications.
Nabertherm GmbH
Bahnhofstr. 20
28865 Lilienthal/Bremen
www.nabertherm.de
Hall 8, Stand 530