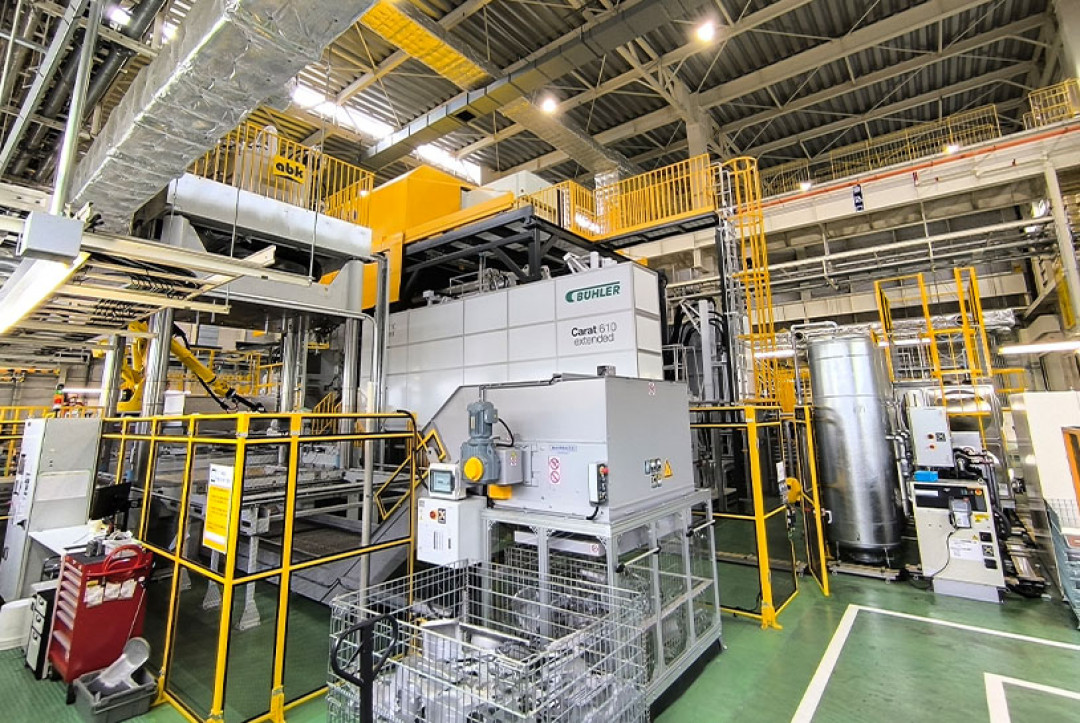
Swiss technology company Bühler Group has supplied Honda Motor Company Ltd. with their first Megacasting solutions. The Japanese automobile manufacturer has invested in multiple Bühler Carat 610 die-casting machines to accelerate electric vehicle (EV) production across its network in North America and meet continued strong customer demand across the region.
Honda is using one of the Carat 610 cells in Japan for research and development, and the others will be operated at the Anna Engine Plant, in Anna, Ohio. In the US, the Carat 610 Megacasting machines are used by Honda to cast the cases for its Intelligent Power Units (IPUs). The first cells have already been installed at Honda’s Anna Engine Plant and production is ramping up.
The IPU case will contain the EV battery module and serve as the main frame structure for the floor of Honda and Acura EVs. They will be manufactured at the Anna Engine Plant, then delivered to the EV Hub in Marysville where the battery modules will be installed. “The IPU case is much larger than anything Honda has die cast before. It will be die-cast in two pieces and welded together,” says a Honda representative. In-house production of IPUs is a first for the company.
Japan established expertise in Megacasting
In Japan, a Carat 610 was commissioned in March 2024 at Honda’s site in Tochigi. This cell is being used for research and development (R&D): Honda is conducting controlled experiments under different casting conditions to ensure and improve the quality of their end products. “Several parameters such as the casting temperature, the pressure, the casting speed, and the cooling rate can be varied in order to examine their effects on the properties of the parts,” says Cornel Mendler, Managing Director Die Casting at Bühler.
The use of various fully-automated peripheral devices, such as spray robots for applying release agents, removal robots for lifting the parts from the molds, trimming presses for removing casting flashes and the cooling basin for regulating cooling processes, enables precise control of the entire casting process and helps to achieve reproducible results. “The R&D cell makes it possible to test process innovations and newly developed parts quickly and efficiently. This rigorous testing allows us to optimize our processes,” says Honda. “The expertise and experience that we gain in Japan will be shared across our production network in North America to support our electrified future.”
Designed for large and complex parts
Bühler has been active in die casting for nearly 100 years and the Carat series is Bühler’s answer to the globally accelerating trend towards larger structural castings in modern car architectures. The two-platen technology with die locking forces of 10,500 to 92,000 kilonewton (kN) is specifically designed to produce large and complex parts.
Megacastings reduce complexity in production by enabling between 70 to 100 parts to be replaced by a single die-cast part. These single-piece castings will generally be produced close to the automotive assembly line, allowing for better integration and reduced transport. Bühler has manufacturing sites for the construction of its Carat machines in Europe, the US, and China.
Featured photo: Bühler Group