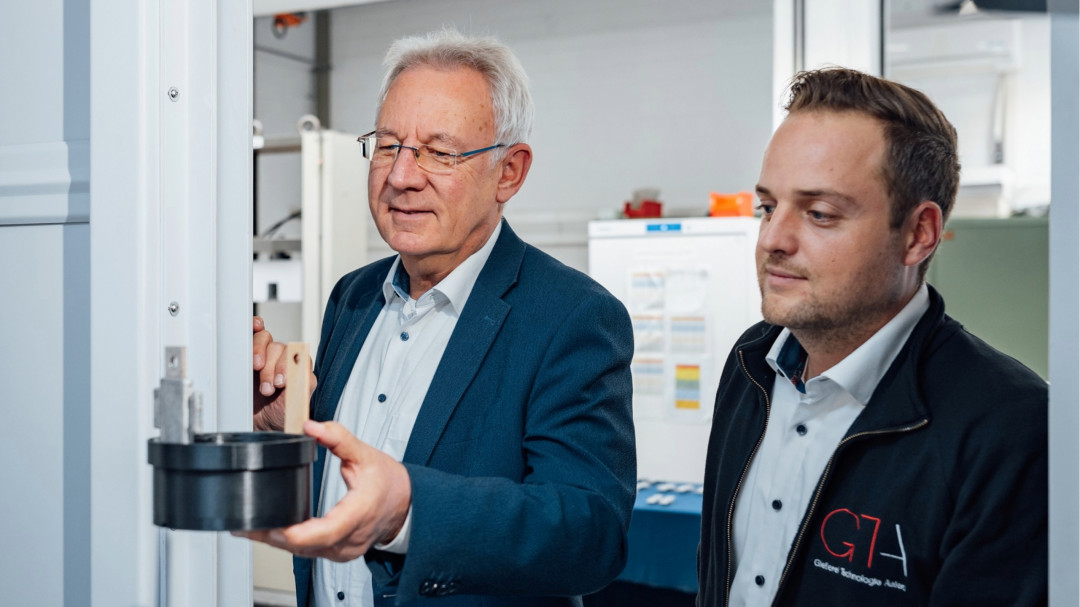
Today, vehicle bodies are made of metal. Wood, on the other hand, is considered a lighter, more climate-friendly option. The research group led by Prof Dr Lothar Kallien, head of the foundry laboratory at Aalen University, has now developed a new casting process. Here, wooden components are encapsulated with a thin layer of light metal. The composite material has optimum properties for industrial applications - such as vehicle construction.
While cars used to be largely made of wood, today wooden components are only used in the interior for aesthetic reasons. The research group led by Prof Dr Lothar Kallien from Aalen University wants to revive this natural material with its physical advantages and low CO2 balance. The scientist sees the process as the future of car body construction: "More wood will be used in cars, I'm sure of it."
Die-casting process combines wood and metal
The team is working on hybrid wooden structures using the die-casting process, combining wooden structures with lightweight die-cast alloys made of aluminium and magnesium. The research group first had to overcome one challenge: During the die-casting process, high temperatures act on the wood, threatening to burn it. The aim is to avoid the thermal damage to the wood core using a special technique: very thin-walled moulding. In principle, this is possible with the die-casting process in Aalen. However, further research is required for this application. This would leave the wood intact and stabilise the component from the inside. The research approach arose from the results of the SmartPro project in the field of lightweight construction, which was funded by the Federal Ministry of Education and Research.
"By combining wood and metal, we obtain a lightweight construction material that significantly improves the rigidity of the component and is also very light," says Dr Daniel Schwarz, a scientist from the research team. "And that's exactly why we want to go back to the natural material - simply because it has so many physical advantages and significantly improves the carbon footprint of vehicle construction." The fact that the material is both light and very stable means that even very large, complex components can be created. Car manufacturers such as Tesla are already working on car bodies that consist of a single part. This saves a number of production steps and specialised robots. The die-cast wooden inserts are therefore lighter, more stable and more environmentally friendly - but are the components also of the right quality? Kallien's team checks this with the help of a computer tomograph. This allows them to examine the new component for defects using X-rays without damaging it.
New lightweight construction solutions are interesting for industry
Cooperation between science and industry is essential in order to develop and implement innovative lightweight construction solutions: research provides new production technologies, while industrial partners define the fields of application and put the new technologies into practice. A number of companies from various sectors are now interested in collaborating with the research group. "In addition to vehicle bodies, our development can also be used in many other areas - for example in chainsaws or aerospace materials," explains Kallien and emphasises: "We are delighted to be working with industrial partners who show us where there is a need in the economy and in which applications our technology could be used."