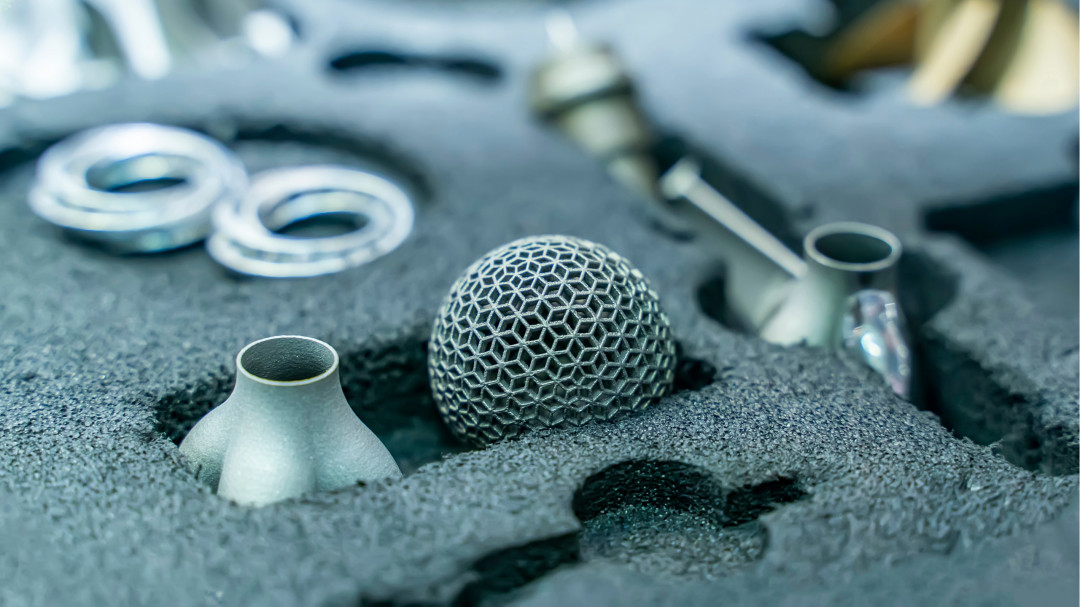
Tools for forming processes are generally made from tool steel and require a specific property profile in order to be used optimally and for as long as possible. Up to now, they have mainly been produced using conventional manufacturing processes such as casting or machining, which results in material loss. To date, tool steels have only been suitable for additive processing to a limited extent. Finding an alloy that has the required properties and can be additively manufactured is the aim of a project at the Chair of Materials Technology (LWT) at Ruhr-Universität Bochum.
Supported by the company Dörrenberg Edelstahl GmbH, doctoral student Julia Hahn will go on the search. The project is being funded for four years by the industrial partner from Engelskirchen in the Oberberg district. "Innovative manufacturing processes such as additive manufacturing require specifically adapted material solutions in order to fully exploit their potential," explains Prof. Dr Sebastian Weber from the LWT. "We are delighted to have a competent research partner at our side for this challenge through this cooperation," adds Prof Dr Christoph Escher from Dörrenberg.
Manufacturing without material loss
Tool steels for forming tools must be particularly hard and wear-resistant and have the highest possible thermal conductivity. "Such alloys do exist, but additive processing is only possible to a limited extent," says Julia Hahn. However, additive manufacturing processes have advantages that the researchers would like to utilise. For one thing, only as much material is needed as the tool will ultimately consist of - unlike with other processes, there are no chips. Additive manufacturing processes also offer the possibility of incorporating complex structures such as cooling channels into tools. They can optimise forming processes and increase the service life of tools. "Certain additive manufacturing processes can also be used to finalise a cast workpiece and coat its surface by using alloys with different properties. In this way, pre-cast forming tools can be optimised and given different local properties. This in turn extends the tool life and improves the forming process," explains Julia Hahn. "In this way, more resilient tools can be produced with a simultaneous cost advantage compared to conventional production processes, and with much shorter lead times for planning and production," says Christoph Escher.
Julia Hahn will begin her search for the optimum alloy with thermodynamic calculations and start from successful alloys. If the calculations are promising, it's then time to experiment: the calculated alloys are atomised into powder using the chair's own atomisation system, which is then processed into samples using the powder bed process or direct energy deposition. In the powder bed process, a laser melts only the powder particles in a metal powder layer that will later make up the workpiece. The remaining powder can be reused after reprocessing. Direct Energy Deposition is similar to build-up welding. Here, the metal powder is applied to a workpiece in a targeted manner using a feed nozzle, where it is melted locally by laser radiation and bonded to the workpiece. The special feature of this process is the simultaneous use of two different alloys, which means that components or coatings with locally different properties can be produced.