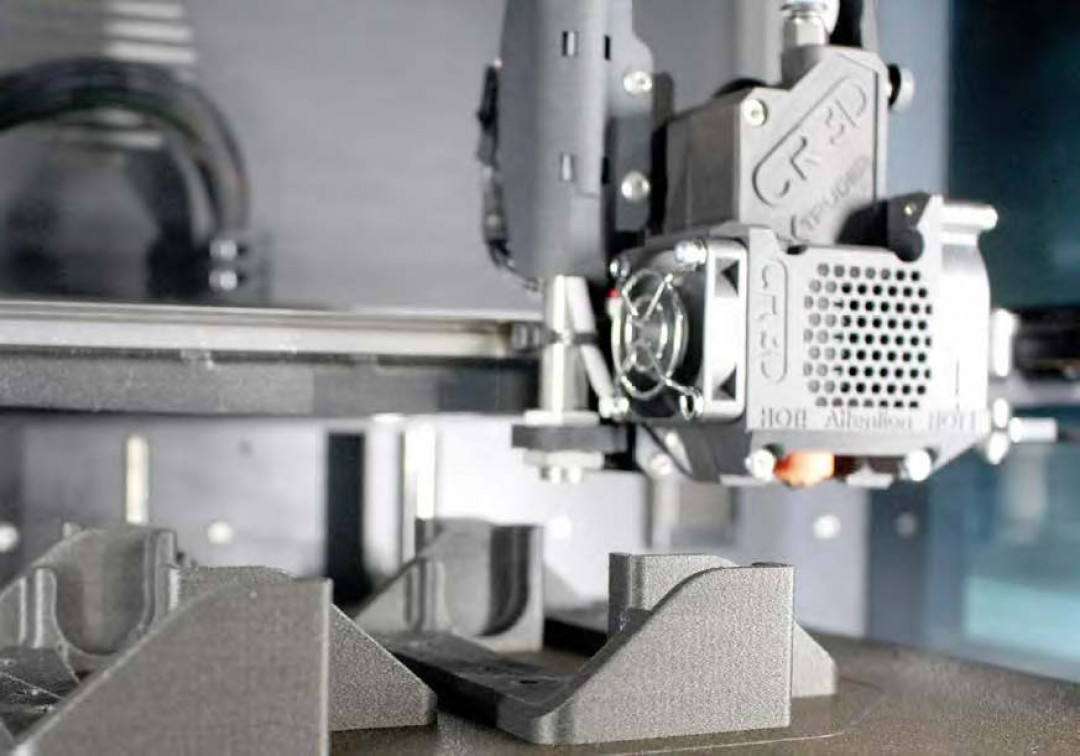
Additive manufacturing is moving into the focus of manufacturers of mobile machinery for construction, agriculture and forestry at Systems & Components, which will be held as part of Agritechnica in Hanover from 12 to 18 November.
In addition to the familiar powder- and wire-based technologies, exhibitors are also working on innovative material combinations to push the limits of 3D printing. For one, they are using binder jetting of sand cores as the basis for high-quality casting of components such as axle housings or wheel hubs. This 3-D mould making with sand has decisive advantages for lightweight construction. In addition, the complexity of the castings can be greater than with typical sand casting because the need for distortion and parting lines is greatly reduced. Off-highway foundries and pattern shops, like original equipment manufacturers, have integrated appropriate pressure equipment into their production lines to enable the ongoing production of sand castings.
However, the full potential of additive manufacturing will be tapped at Systems & Components and Agritechnica primarily by agricultural machinery manufacturers and their OEM partners, who are now printing various components directly. Technologies such as fused deposition modelling (FDM) or selective laser sintering (SLS) make it possible to implement near-series materials in prototypes and pre-series components that can be transferred to applications in large-scale industrial production. Special features offered by additive production include flexible damping elements made of thermoplastic polyurethane (TPU), engine covers made of high-strength fibre-reinforced plastic or assemblies that allow for more degrees of freedom when equipping the driver's cab. 3D printing can also be used to produce components that cannot be manufactured in one piece using injection moulding.
The choice of the right 3D printing material is particularly important in additive manufacturing. Even though plastics allow components in almost all facets, metal is currently one of the most sought-after materials for additive manufacturing processes. Not surprisingly, its properties make it the ideal choice for demanding applications in terms of performance and strength. Metals can withstand the stresses, temperatures and pressures of off-highway applications thanks to their strong crystalline microstructure - enabling the production of parts with the strengths required for drive components in mobile machinery. Aluminium in particular has the potential to enable resource-efficient lightweight construction.
Metal Binder Jetting (MBJ) is also one of the up-and-coming additive manufacturing processes. John Deere, for example, uses HP's Metal Jet S100 technology to produce valves that function in extreme weather conditions and are used in tractor fuel systems. Similar to selective laser melting of metal (SLM), the process uses a powder bed that a material sled deploys in the build space, but which is not melted by a laser beam. Instead, a light-curing bonding agent (the binder) is printed onto defined zones via a print head to produce the component. It binds the particles everywhere where solid metal is to be created later. In this way, the green compact is created layer by layer. This must then be debinded and sintered - and the component is finished. According to the manufacturer, HP's 3D printers can precisely apply up to 630 million nanodroplets of the binder to the powder bed per second. John Deere also uses the technology for prototypes to test and fine-tune components such as windscreen brackets.