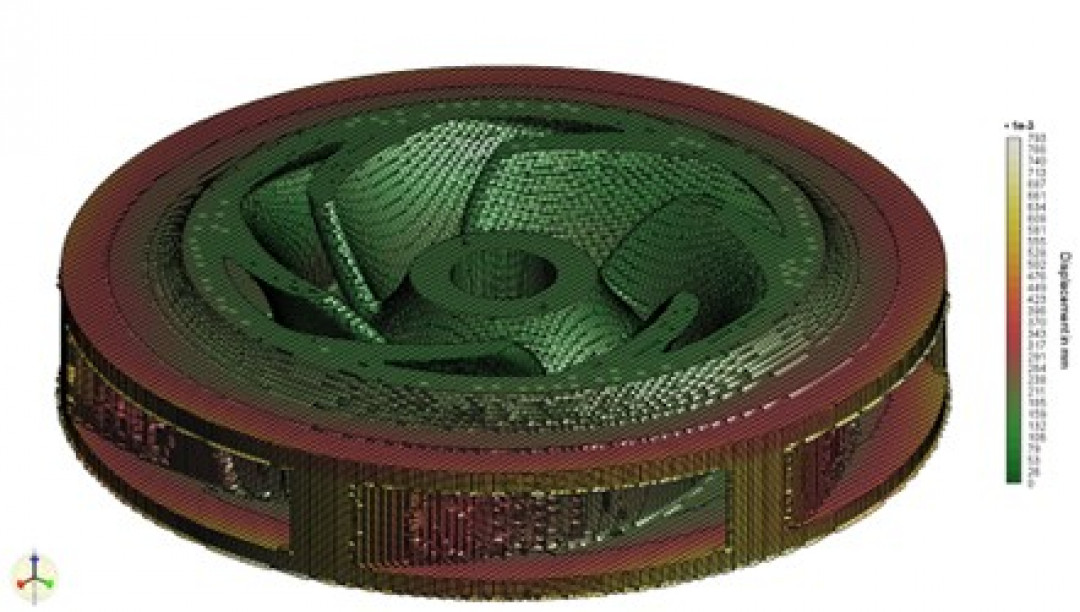
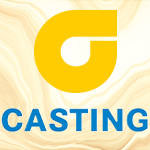
The primary appeal of the developing additive manufacturing (AM) technology is the potential to reduce production times while enhancing part quality. A major impediment to the realization of this promise is the lack of accuracy in design. Companies often need to go through numerous iterations of a prototype, each substantially adding to the cost, to perfect a single part. Finnish technology giant Wärtsilä leveraged Amphyon’s metal additive simulation capabilities to overcome this problem and get an AM-built pump impeller right the first time.
By Nils Keller
Impellers are the rotating component of centrifugal pumps that accelerates fluid outward from the center of rotation. From the energy to the marine industry, they’re widely used and often customized for different applications. This is why manufacturers usually produce impellers in large numbers to ensure a substitute is always readily available.
While pump impellers are common, they’re also inordinately expensive. The high costs of manufacturing and storage have driven companies to seek out more affordable alternatives and explore the new world of possibilities created by additive manufacturing.
One such forward-thinking business is Wärtsilä. Born in Finland almost 200 years ago, Wärtsilä has established itself as a leader in adopting innovative technologies and lifecycle solutions for the marine and energy markets. With such a formidable engineering heritage, it’s no surprise the company spearheaded the move to optimize the impeller production process. Their visionary impetus resulted in an AM-built pump impeller that’s lighter than the standard but just as robust.
The impeller had two iterations, each delivering lighter, and withstood hundreds of hours of testing with no breakage, failure or misalignment from standard operations. The successful production of a pump impeller makes AM’s cost-saving promise one step closer to reality.
Replacing traditional manufacturing methods with AM also allows companies to reduce their spending. Wärtsilä would no longer need to prototype by casting, a process that normally requires tooling parts that cost tens of thousands of euros. Spare parts could be produced on-premises, as the need arises, making long lead times and expensive storage requirements part of the past.
To manufacture the impeller, Wärtsilä joined forces with three other manufacturing specialists – Oqton, the developer of metal additive simulation software Amphyon, an engineering design software company nTopology, and metal additive technology partner SLM Solutions. The collaboration resulted in several ground-breaking achievements, including printing challenging rotating parts, and significant reductions in manufacturing lead time and post-processing cost.
“This work has demonstrated the power of sharing top-notch expertise of different companies working on a common goal,” Francesco Trevisan, AM expert at Wärtsilä, said. “This impeller has disclosed several technical innovations and provided beneficial values to the final application on marine engines. We have achieved a lightweight component we would have never imagined creating before this project. This application creates new sparks for more AM applications in the marine industry”.
Simulation as the key to success
Amphyon was instrumental in bringing the project to fruition. By simulating the actual AM build and allowing users to pre-deform the model to compensate for any distortions arising during production, Amphyon took all the guesswork out of the process. Normally, the process of perfecting a metal printed model without simulation software predicates on iteration – the manufacturing of various versions of a component until the desired result is achieved. However, in metal AM, each iteration comes at a great additional cost. Amphyon’s ability to simulate the metal additive process and pre-deform designed models enabled SLM Solutions to achieve an accurate design with fewer part versions and lower costs.
The marine impeller is also smaller in mass than a conventionally manufactured one, which was achieved with nTopology and SLM’s Free Float technology. nTopology enabled engineers to design an internal geometry and lattices that result in reduced weight while maintaining stiffness. The lattice structures were also aligned with the cylindrical axis, complimenting the rotational nature of the impeller. A structural analysis was also performed with the goal of hollowing and thickening the interior lattice beam based on stress results.
The design was further adjusted in Amphyon to prevent deformation. To calculate the warping of the pump impeller, Oqton’s metal additive simulation software considers the thermal stresses of the build process, stress relief, and support removal. Instead of meshing the complex lattice structures, a new homogenization approach was used that significantly reduced the calculation time. The final analysis took only 1 h 35 min on a regular CAD workstation. The result was a distortion-compensated, or pre-deformed model, which allowed Wärtsilä to get a near-net-shape lightweight part.
Finally, Free Float technology was used to print surfaces with an angle of fewer than 45 degrees. These kinds of surfaces normally require support structures that are removed in post-processing, but with a complex part such as a pump impeller, removing the supports with tools wouldn’t be possible because they are inaccessible. In the case of this pump impeller, SLM’s smart vector enabled printing surfaces with an angle of 20 degrees.
Minimized weight, maximized performance in one part
The resulting pump impeller was tested in a real-scale laboratory engine with multiple measurements to indicate the performance, at different engine loads. Real environmental conditions, such as 120 ⁰C temperature and rotational speed over 2600 rpm, were applied. "With the shared knowledge of these four companies, we created an application that takes AM in the energy sector to the next level,” Lorenz Kropholler, project manager at SLM Solutions, said. “The combination of innovative new tools in the field of design, pre-deformation and production generated a part that stands out on many levels. Minimized weight, maximized performance and a lead time of just days are all combined in one part".
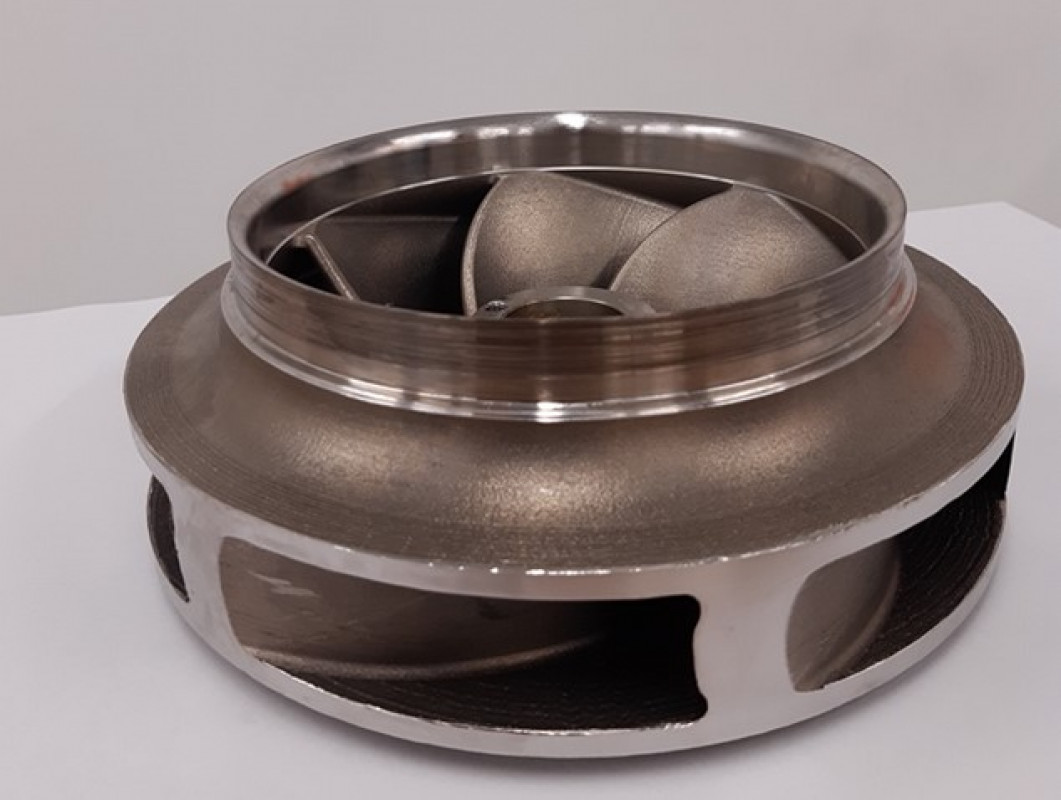
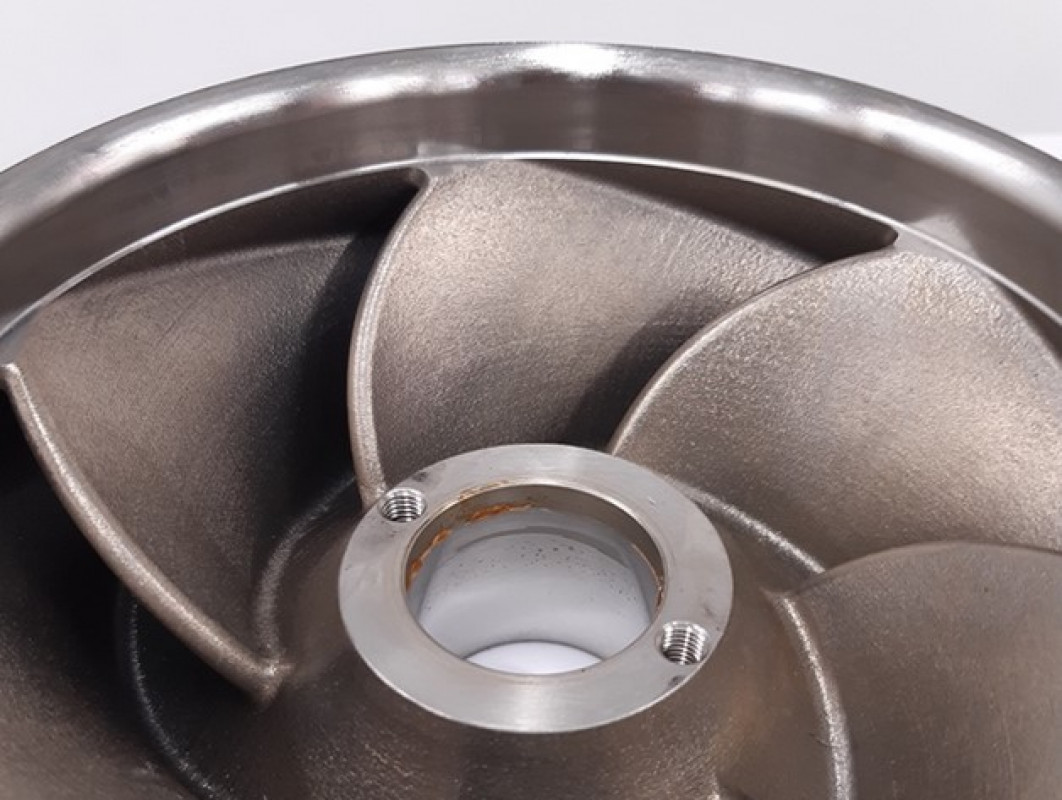
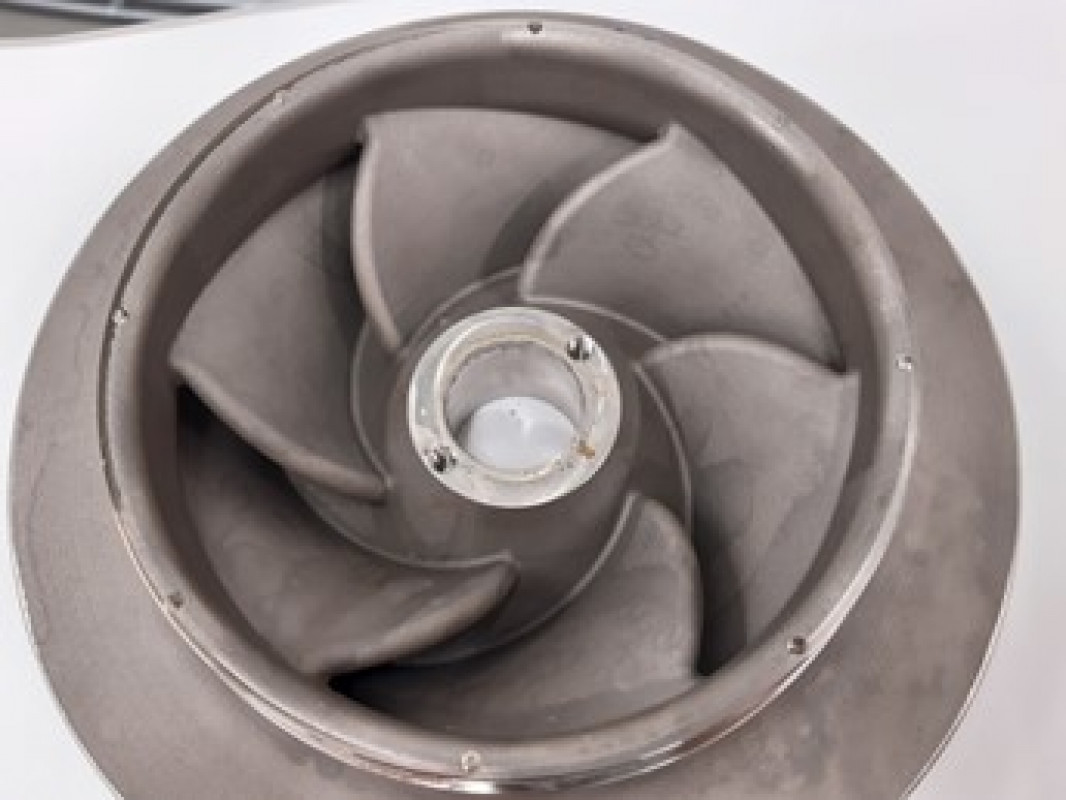
About Wärtsilä
Wärtsilä is a global leader in innovative technologies and lifecycle solutions for the marine and energy markets. Their dedicated and passionate team of 17,000 professionals in more than 200 locations in 68 countries shape the decarbonization transformation of our industries across the globe. In 2021, Wärtsilä's net sales totalled EUR 4.8 billion. Wärtsilä is listed on Nasdaq Helsinki. For more information, visit www.wartsila.com
About SLM Solutions
SLM Solutions is a global provider of integrated metal additive manufacturing solutions. SLM Solutions is home to the world’s fastest metal additive manufacturing machines boasting up to 12 lasers and enabling build rates up to 1000 cm³/h. SLM Solutions is a publicly-traded company headquartered in Germany, with offices in Canada, China, France, India, Italy, Japan, Singapore, South Korea, and the United States. For more information, visit www.slm-solutions.com
About Oqton
Oqton accelerates smart manufacturing by providing comprehensive software solutions for additive manufacturing, 3D scanning and robotic welding, helping industrial and healthcare organizations drive innovation and increase efficiency. The company's additive manufacturing software enables full traceability and visibility across the enterprise and provides AI-powered capabilities for image segmentation, additive design, print preparation, MES, additive inspection and simulation. Global manufacturers use Oqton's software to automate robotic welding to increase productivity. The company's industry-leading Geomagic suite provides the foundation for 3-D scanning solutions for reverse engineering and inspection applications. Oqton is supported by partnerships with machine and scanner vendors, software partners and ERP/CAD/PLM integrations. For more information, visit www.oqton.com