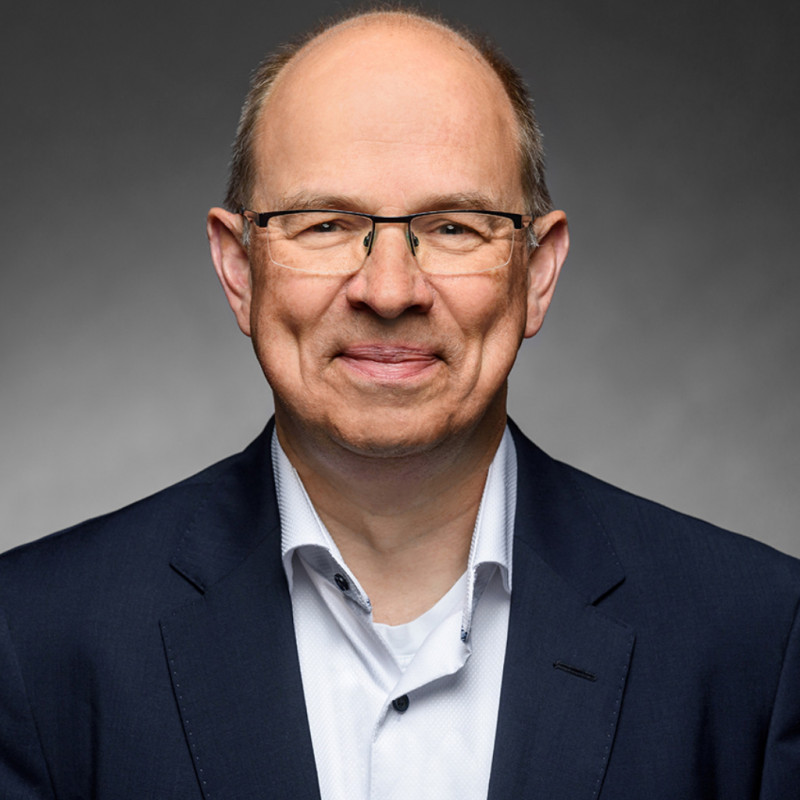
Industry 4.0 has a key role to play in systematically safeguarding and further developing value creation in Germany. It can help to overcome current industrial and socio-political challenges. In this interview, Dr Marc Hüske talks about sustainability, technological sovereignty, interoperability and the role of people. Hüske is a member of the Industrie 4.0 research advisory board coordinated by acatech and head of the VDMA's Manufacturing-X forum.
Mr Hüske, the climate crisis highlights the need for innovation in the context of ecological sustainability in the creation and use of products and services over their entire life cycle. What specific steps or approaches should be taken to research and implement sustainable Industrie 4.0 solutions?
The current challenges are immense and in view of the climate crisis, we should take advantage of the technological opportunities offered by digitalisation and automation with regard to ecological sustainability – supported by the exponentially growing volume of data available to us, which is also a consequence of the EU data regulation. New data-based business models will emerge throughout the entire product life cycle, from raw material extraction to recycling, which will demonstrably promote the resilience, sustainability and competitiveness of industry. The consequences are greater transparency, efficient use of resources and the ability to respond more quickly to disruptions in supply chains. Particularly when it comes to important topics such as decarbonisation or the circular economy, sustainable process optimisation through cross-process control chains, for example, plays a major role. The implementation of Industry 4.0 technologies also helps to reduce material consumption through more precise manufacturing methods. Business models based on providing services instead of selling products can reduce resource consumption and extend the life cycle of products; just think of certain leasing or sharing models. In the area of energy efficiency and emission reduction, for example, intelligent energy management systems for monitoring and optimising energy consumption in real time can minimise energy consumption and maximise the use of renewable energy sources.
National and global influences on the economic system have further increased the relevance of Industry 4.0. Among other things, the coronavirus pandemic and the Russian war of aggression against Ukraine, combined with the scarcity of important resources, have highlighted the vulnerability of existing value chains and networks. At the same time, the technological sovereignty of the German economy seems to be increasingly being lost in various areas in the face of international competition. How can Industrie 4.0 be used to increase the resilience of value creation and the technological and strategic sovereignty of Germany and Europe, and what role do interoperable, digital ecosystems play in this?
Precisely because technological sovereignty is such an important topic in the EU and Germany for being able to strategically assert oneself in international competition, especially against the USA and China, initiatives such as Industrie 4.0 are needed, along with the development of a European cloud infrastructure like GAIA-X and data space initiatives like Manufacturing-X. Interoperable digital ecosystems play a central role in strengthening the resilience of value creation and the sovereignty of our business location through Industry 4.0. If a pandemic, war or other external influences suddenly change demand and resource availability, companies will be required to be highly flexible. The industrial data space, which provides a trusted infrastructure for sharing data, enables companies to flexibly and quickly adapt their supply chains and production processes in a data-driven way. Value chains thus become more robust and generally less susceptible to interruptions if potential disruptions can be detected early and efficiently managed through real-time data analysis. Manufacturing-X enables the seamless integration of different industrial systems across company and national borders, which not only promotes collaboration but also new business models and value creation potential. This applies particularly in the area of key technologies such as AI and IoT. Data sovereignty remains with the company, so that each company can reap the full benefits from its own data. Open standards and interoperability ensure that collaboration works particularly well within Europe and with international partners, which reduces dependencies and strengthens Europe's position in the global competition, as well as its technological sovereignty.
In the context of Industry 4.0, the optimal integration and support of people through the appropriate design of work and production processes is addressed from the outset. How can it be ensured in the future that people will continue to be at the centre of this development?
That's a shot in the dark, but I am convinced that work and production processes will not develop completely independently of people. There will be some kind of coexistence. Augmented reality and virtual reality will certainly play a role when it comes to human-machine interaction. Both technologies will help visualise complex processes and make them easier to understand. One example of their use is in training or for service staff. However, it is essential that employees have the necessary skills to work with new technologies such as AI, robotics and data analytics. Lifelong learning, curiosity and a willingness to embrace new things are part and parcel of this. It is the job of managers to support this transformation process constructively. On the other hand, production systems should be designed to be so flexible and adaptable that they can be aligned accordingly in the face of ever faster changing market conditions and customer requirements. By analysing data from production processes, workflows can not only be optimised, but it can also be ensured that the individual strengths and weaknesses of employees are taken into account, which accommodates the interaction between man and machine.