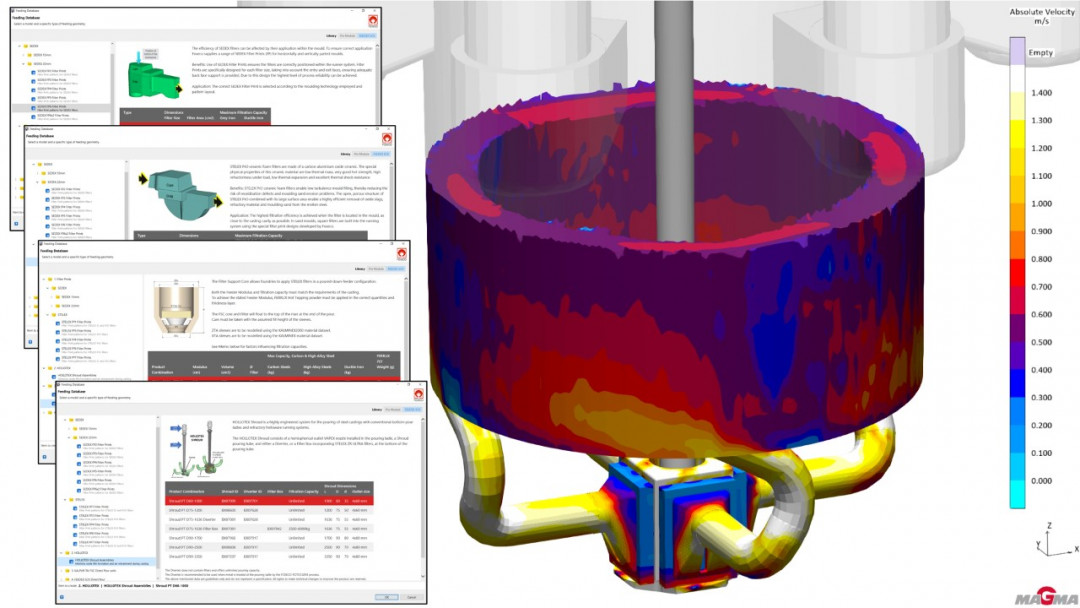
FOSECO, the foundry division of Vesuvius and a world leading supplier of casting consumables, and MAGMA, a world leader in casting process simulation and virtual optimization, celebrate the 20th anniversary of their strategic alliance with the release of a new version of the FOSECO Pro module.
In 2003, the two companies agreed to join forces to support their mutual customers with their complementary product portfolios. At that time, FOSECO committed to implement MAGMASOFT®, MAGMA‘s simulation program, in its application teams worldwide. To complement this initiative, MAGMA developed the first version of the FOSECO Pro module, a product database available exclusively to our joint customers. The FOSECO Pro module was the first database in the world to cover the main FOSECO feeding & filtration products, in terms of their 3D geometries and the modelling of their performance during the casting process. This allows the user to quantitatively consider the FOSECO product range in their simulation analyses.
The FOSECO Pro module, successfully used by a large number of foundries worldwide, has now been upgraded to meet growing demands in terms of usability and support for new FOSECO products.
The new version of the Pro module provides MAGMASOFT® users with a state-of-the-art database that is fully integrated into the new MAGMASOFT® 6.0 user interface. The database allows the user to review and select from the available FOSECO product range, loading 3D assemblies of the respective geometries and product properties. The module continues to be to be fully compatible with MAGMA’s unique Autonomous Engineering capabilities, enabling users to select the best possible products for the given quality requirements.
New capabilities have been added to select not only suitable filters, but also the geometry of the recommended filter coreprints. For steel foundries, the Pro module will now offer the selection of innovative FOSECO products such as the HOLLOTEX shroud pouring system, with the complete assembly of diverters or filter boxes conveniently available. This will assist steel foundries in the design of gating systems and the optimisation of their casting processes using simulation.